
The Factory of the Future is a connected world of everything.
We will explore the benefits of IoT in manufacturing, including asset monitoring and utilization, quality control, predictive analytics, automation, safety and compliance, OEE visibility and productivity, and more.
With IoT solutions, companies can achieve their Industry 4.0 goals and increase their bottom line.
What is the Internet of Things (IoT)?
The Internet of Things (IoT) is the network of physical objects, people and other assets that are connected to the internet. IoT allows you to collect data from devices and analyze it in real time.
The goal is to make processes more efficient by optimizing performance and reducing costs.
IoT can be used to monitor machines in factories, track inventory at warehouses or even monitor traffic conditions on roads. It’s also used for home automation tasks like turning off lights when you leave a room or adjusting your thermostat based on your location inside (or outside) the house.
IoT Ecosystems
An IoT ecosystem refers to the network of devices, sensors, software, and services that are interconnected and work together to collect, analyze, and act on data.
They are often utilized to gather data on connected assets, and tools in order to gain real-time insights into their condition for predictive maintenance purposes.
The goal of predictive maintenance is to detect and address problems before they cause equipment failure, downtime, or safety issues.
By predicting maintenance needs in advance, organizations can schedule maintenance during planned downtime, minimize the impact of maintenance on operations, and extend the lifespan of equipment.
Connected Products
A smart, connected product (also known as a smart object or SCoT) is a product, asset, or other object embedded with processors, sensors, software, and connectivity that allows data to be exchanged between the product and its environment, manufacturer, operator/user, and other products and systems[1].
Smart, connected products enable the comprehensive monitoring of a product’s condition, operation, and external environment through sensors and external data sources[2].
This technology stack provides a gateway for data exchange between the product and the user and integrates with other systems to enable a new level of customer experience[3].
Connected Factory
Similar to connected products, a smart, connected factory is a digitized manufacturing facility that uses connected devices, machinery, and production systems to continuously collect and share data.
This data is then used to inform and improve processes and proactively address any issues that may arise.
It is an interconnected network of machines, communication mechanisms, and computing power, which uses advanced technologies to analyze data, drive automated processes and learn as it goes. It uses the sensors and software of the connected products to bring together the factory floor.
A connected factory is implemented to track the overall equipment efficiency or effectiveness (OEE) of the factory.
A smart connected factory is the telltale sign of a manufacturing floor that is functioning at its most optimal ability.
Having access to data insights regarding production health helps companies optimize earnings and minimize production downtime.
Augmented Reality
Integrating augmented reality (AR) with IoT involves using sensors and other IoT devices to collect data from the physical world, which is then used to augment the user’s experience in the digital world.
For example, AR can be used to display real-time data from IoT sensors, such as temperature or humidity, on a user’s mobile device. When a cell phone or tablet uses Augmented Reality (AR) to display data, it overlays virtual information on top of the real-world view seen through the device’s camera.
This can be particularly useful in industrial settings, where workers can use AR to monitor the performance of machines, detect any issues immediately, and take corrective action. This kind of data can be turned into a Digital Twin.
Digital Twin
With a Digital Twin, you create an exact replica of a working product, process, or service as a simulated model in a virtual space that performs under real-world conditions.
A Digital Twin in manufacturing helps companies find performance issues, schedule predictive maintenance, reduce downtime, and minimize warranty expenses.
This allows anyone to take a digital version of your factory with you anywhere in the world and know the exact, real-time data of how it is functioning. This is extremely helpful for decision-makers who often travel and need to know how their factories are doing.
Additionally, a digital twin of your factory helps maintenance teams find precisely where an issue may have occurred by giving them visual prompts of where the problem is originating from.
The Benefits of IoT in Manufacturing
IoT has a plethora of benefits for manufacturers that overall saves companies time and money, and solves frustrations with outdated processes and siloed data.
Bellow are different ways the IoT solutions could benefit your production process:
Asset Monitoring & Utilization (AMU) & Real-Time Production Performance Monitoring
Gain real-time insights from connected assets and legacy systems such as your PLM and ERP systems to align your IT and OT systems
Make more informed decisions faster
Increasing flexibility and agility
Monitoring the status of inventory in real-time
Quality Control
Monitoring Distributed and Outsourced Processes
Spare parts management
IoT sensors allow organizations to gauge the specific use and deploy practices for more effective usage of resources.
Machine Learning & Predictive Analytics
By integrating machine-learning capabilities there is a whole new level of predictive intelligence brought to the factory floor – identified problems and resolved issues with minimal impact on operational performance. Other benefits include:
Detect problems before they occur
This helps to maximize factory production utilize data analytics to perform predictive maintenance
Optimizing Maintenance Schedules
Automation & Connected Work Cells (CWC)
In manufacturing, many processes are streamlined with IoT technology. For example, one IoT strategy is to use Automation. With IoT, using sensors allows you to automate certain tasks such as temperature monitoring or product tracking.
This means less time spent on manual labor and paper-based processes while increasing productivity simultaneously!
Safety & Compliance
Making sure that machines are running at a safe capacity and within the compliance standards creates a well maintained work area that brings employee satisfaction and confidence in a safe workspace.
All these things can be tracked through IoT technology, along with others:
Increasing energy efficiency of machines
Reduce human errors
Ensuring Products Comply with Set Standards
Increased employee and customer satisfaction
OEE Visibility & Productivity
A factory enhanced by IoT solutions offer complete visibility into all of your factory operations. You can see all of your work orders, lines, and all critical KPIs through dashboards that pull together
IoT sensors allow organizations to gauge the specific use and deploy practices for more effective usage of resources.
Cost reduction
Increase bottom line
Decreased Machine Downtime
Optimizing Factory Production
Reduced lead time
Improved efficiency
Improvement of Operational Performance
These are just some of the many ways companies can reach their goals with Industry 4.0. With out-of-the-box solutions or even custom IoT apps, the possibilities are endless.
Implementing IoT
The first step in implementing IoT in manufacturing is to identify your goals. Are you looking to improve efficiency, reduce waste or increase profitability?
Do you want to improve customer satisfaction by delivering products on time, or do you want to create new revenue streams with data collected from connected devices?
Once you’ve determined what kind of impact IoT can have on your business, it’s time to evaluate the current technology that’s not only available but that easily integrates with your current systems and shop floor.
Finally, develop an action plan for implementing these strategies broken down into digestible phases. It’s critical to understand what solutions fit best and most align with your unique business and prioritized initiatives.
Common Challenges
We hear from companies all the time regarding what challenges they feel stops them from implementing IoT in manufacturing.
The first is cost. However, with any good investment, the benefits of using IoT solutions offset the cost. While IoT ROI doesn’t happen overnight, the full impact IoT has on manufacturing organizations is tenfold.
NORMA Group met with EAC experts to understand what sort of impact an IoT initiative would have on their business growth and determined the challenges were well worth the wait – something we find other companies can relate to. Another early adopter, JR Automation was able to save $1.4 million by investing in IoT.
Security
The second common challenge that comes with implementing IoT is security. This includes both physical and data security issues that need to be evaluated and addressed before implementing any type of data management change.
Finding a solution with integrated automated tools and detailed monitoring is key to preventing attacks. Check out this article that talks further about data security and how PTC’s Kepware supports cybersecurity.
Data Management
Another challenge we see is considering how well your organization will be able to manage the new information coming from all over your facilities. It’s key you create a plan to integrate the new data flow into your existing systems.
With user-friendly IoT-connected solutions like PTC Thingworx, data is captured, consolidated into a dashboard, and presented in a consumable visual format for real-time insights.
Hardware
Another consideration is requirements: What sort of hardware do you have to support that software change? Replacing or updating existing systems and hardware to increase efficiency may be necessary to keep up with the fast pace environment of shop floors.
There is no doubt that these are important things to consider when making enterprise-wide changes. While implementing IoT can feel difficult and intimidating, it does not have to be.
EAC has a number of business assessments that can help you evaluate your current state and create a highly strategic roadmap to successfully scale your digital transformation initiatives.
Ultimately, Digital Transformation is a game changer for manufacturing companies who are unsatisfied with the “status quo” – and IoT will open up major opportunities for long-term success and sustainable growth that would not have been possible without making changes.
Connected Future
Empower your organization with enhanced connectivity to your products, systems, and customers.
IoT can provide significant advantages for manufacturers across the enterprise, but it is important to properly evaluate, plan and implement the right technology and the right solution at the right time in order to maximize the potential benefits.
Our IoT consulting and connect services provide comprehensive support from extracting valuable insights, and developing strategic plans to executing and implementing efficient IoT solutions that accelerate your digital transformation.
Chat with one of our experts on how we can help you identify the best IoT solution for your needs and how we can help your company implement it the right way.
AR and IoT are beginning to transform the way organizations are interacting in their industrial environments.
With the ability to integrate technology everywhere, products, processes, and people now have the ability to be connected like never before, allowing enterprises to drive product and service differentiation and promote operational effectiveness, workforce productivity, and unmatched quality.
Some might refer to this concept as the idea of digital transformation…but what does that really even mean? This article breaks it all down for you.
Digital Transformation with IoT and AR.
Today, innovative Augmented Reality tools have the ability to connect with powerful IoT data while working seamlessly in a service and training environment. With a mobile device or AR headset, technicians can easily learn to work in tandem drastically reducing training time and downtime simultaneously.
To better understand a concept of ‘digital transformation’, I’ll walk you through a real-life scenario involving one of our customers.
For this specific customer, the combination of AR and IoT has drastically improved the efficiency of their operations.
With the use of an AR application, our customer is able to provide their off-site workers with a digital model of one of their products immediately.
Placed alongside the digital model of their product, they are also able to see real-time data from the physical product that is off-site or working in the field.
This is possible because their AR experience also leverages a connection with their IoT platform, known as ThingWorx.
Their ThingWorx IoT platform connects to their disparate data systems, such as their ERP and CRM systems. It also connects to their PLM software, which provides them with the ability to pull a configuration from their PLM software, known as Windchill. This allows them to showcase unique product information, such as the VIN, model, customer and purchase information.
By having this data available and in context, remote technicians are better informed and empowered to make the best decisions possible.
As technicians launch their AR experience, they are able to see step by step instructions on how to repair or service the specific product.
They are also able to see warnings and replay steps that are integrated into the AR experience so they can be assured they are working in a safe environment without missing any procedures.
With the additional use of Vuforia Chalk, a remote video assistance app, employees are also able to instantly access remote subject matter experts or SMEs who can answer questions related to the experience and interact with the experience directly by drawing on the screen.
Finally, with time tracked throughout the experience, this service data can then be sent back to their ThingWorx IoT platform to assess performance, training, and to improve the CAD design leader.
By combining the use of AR and IoT, training and servicing is no longer hindered by traditional learning for our customer. Instead, their technicians are able learn from an experience that is enriched with data and context.
By leveraging ThingWorx, our customer is able to merge the digital and physical worlds of service providing their organization with an efficient and productive work environment.
This is the idea of digital transformation.
Curious how digital transformation might apply to your organization? We would love to have a conversation. Click the banner below to learn more.
If you have Windchill, a PLM (product life cycle management system from PTC), odds are it’s where your organization stores a lot of really great product data and information. It also means there’s a high likelihood many employees in your organization need access to that valuable product information.
But what happens when people within your organization need to access valuable product information, but they aren’t necessarily veteran Windchill (or PLM system) users? What happens when your ‘casual Windchill users’ only want to quickly get to the information but simply don’t want to be “Windchill users”? 90% of the time this scenario involves your experienced Windchill users being disrupted by requests to pull product information.
Right at this point – exactly when people in your enterprise need access to information in systems they don’t use on a daily basis – is when you lose efficiency, productivity, and revenue. This cross-departmental disruption leads to wasted time, and wasted time leads to wasted money. PTC realized these challenges and created a solution to combat complicated enterprise system interfaces, varying user needs, and disparate enterprise data sources – It’s called ThingWorx Navigate.
To make Windchill PLM, or any PLM information more accessible and solve disruption challenges, PTC designed ThingWorx Navigate role-based applications (apps) that allow users to easily access and consolidate information from secure systems like ERP, MRP, CRP, and PLM systems like Windchill. For instance, by using these applications, a tool designer could call up drawings without having to go through the whole interface of Windchill. The applications pull up windows to look directly into systems, without forcing a user login in and navigate complex product design or enterprise planning systems.
For example, by using PTC’s ThingWorx solution, a tool designer could simply type in a drawing number he or she was looking for on the PTC ThingWorx Navigate application, and the drawing files would pop-up instantly on the screen. These simple product data navigation features also work with product information that purchasing, quality, or any other departments might need access.
PTC’s ThingWorx Navigate applications make it easy for anyone…ANYONE in an organization to obtain product information without having to be a Windchill system expert. One of the great things about these role-based applications is – depending on who you log in as – the apps can be set up to determine what type of information access someone has, as well as what types of product info an employee can access.
For instance, someone on a shop floor could access ThingWorx Navigate applications, and with a simple click in a window would display all the information they need about a drawing. Or perhaps someone only needs to see bills of materials, they could do that in one location by accessing a ThingWorx Navigate application. Just like PTC Windchill, PTC Navigate is a web-based application. This means all an organization really needs is a web browser and a login and instantly anyone can start working.
ThingWorx Navigate applications are also completely customizable. This allows your organization to control exactly what displays on the search screens, as well as, how that information would be delivered to your users. In fact, PTC even created a Thingworx Navigate Productivity calculator to demonstrate how much money enterprise collaboration can save a business. It even lets you estimate your exact company’s potential annual productivity savings!
Bottom line, there really are a lot of great benefits that come along with being able to easily deploy Windchill access throughout an enterprise in a unique and stress-free way. And remember, ThingWorx Navigate also integrates with other enterprise systems, not just Windchill.
But wait…there’s more!
You can make the user experience even better by implementing ThingWorx Navigate and extending functionality and configurability with EAC Productivity Apps. In case you are not familiar with us, our company (EAC Product Development Solutions) specializes in transforming the way companies design, manufacture, connect to and service their products.
One of the ways we do this is through implementing, maintaining, and helping customers with PTC Windchill product lifecycle management systems. Being the Windchill experts that we are, with extensive years of experience (over 23 years to be exact), we work with hundreds of organizations and their PLM systems. This is precisely how we know the need many manufacturing organizations have to extend enterprise system data and capabilities even further!
Working with our Windchill customers over the years, we recognized patterns of system requests and capabilities that just didn’t seem to be specifically addressed by existing solutions. We recognized and researched system challenges that many organizations tended to face with their PLM systems and realized the need to help organizations quickly deploy Windchill, increase user adoption, and capitalize on system functionality. After all, we live in a world obsessed with speed and efficiency. So, to quote the wisdom of Daft Punk, we needed to make complex PLM systems Better, Faster, and Stronger.
Furthermore, we realized valuable data our customers acquired from their other disparate enterprise systems never seemed to be tied together with product data from PLM systems. This was increasing our client’s risk of transferring obsolete inaccurate data. With that knowledge, we knew our solution needed to be able to connect multiple streams of data from different locations and enterprise systems, and even different databases.
All these reasons drove us to develop what we refer to as EAC Productivity Apps. They help organizations quickly advance and capitalize on Windchill PLM capabilities. Although EAC apps are different from Navigate applications in many ways, what I believe really sets them apart is how they use and leverage the concept of data mash-ups. Multiple sources of information brought together to simplify a role-specific workflow.
EAC productivity applications take product data and information from a variety of different systems and transform that data into an easily consumable visual dashboard for any user. Essentially, our apps create a way for organizations to easily connect data from multiple enterprise databases, bring it into one accessible location, and tailor it to the needs of a specific user. This allows any user to easily have all the information he or she could desire with a few simple clicks.
EAC apps also help users access product information, search for information, get bill of material reports, create and manage other related documents, and look at associated parts.
These days product data is everywhere. Everyone seems to collect it, have a lot of it, but the question remains; how exactly can you ensure your organization’s product data is being put to good use?
It’s time to take your product development one step further by providing role-based data access, connecting your enterprise systems, and learning how to make the most of your product data. I am going to explain exactly how easy that is to do.
The current state of product data
Companies today have many different roles that require access to product data. This may include people outside of the typical roles of which you may be thinking.
Departments such as engineering, manufacturing, that’s a given, but expand your thinking to include operations, purchasing, and marketing. They all need data access in order to edit and consume information. Think about sourcing…I’ll stop there, but you get the idea.
Let’s focus on the engineering department for a moment.
People could be involved from the mechanical side, the electrical side, or even a quality standpoint. Beyond that, people need to either contribute or consume information that could include manufacturing, service, sales, and more.
Product data game-changers
Product data silos limit productivity – PTC & EAC have the answer.
PTC ThingWorx Navigate was designed to address data accessibility problems by providing simple role-based apps that deliver just the right information to different groups (or departments) in the way that they need
When non-engineering colleagues need access to vital information, they typically interrupt an engineer or designer with a request. ThingWorx Navigate eliminates that distraction and “double-billing.” Through role or task-based self-service applications, data can be securely shared with a team. That way non-expert teams can use a simplified user interface to access the product data they need, right when they need it.
To help accelerate product development processes and take product data even further, our company (EAC Product Development Solutions) has also created what we call EAC Productivity Apps that work alongside ThingWorx Navigate apps.
So what’s the difference between ThingWorx, ThingWorx Navigate and our EAC Productivity apps?
This is a great question- I am going to try and paint the picture for you.
First, it’s important that you understand what ThingWorx is and how it is different from ThingWorx Navigate.
ThingWorx is the proper name of PTC’s Internet of Things (IoT) platform comprised of 5 components; foundation, industrial connectivity, analytics, studio,
The foundation component is the heart of the ThingWorx loT platform used to make connections to ‘things’ which could be machines, products or software systems or pretty much anything with an IP address and a communications interface.
User interfaces to the data coming from these connections are displayed on websites called ‘mashups,’ created with ThingWorx foundation. You might know these perhaps as ‘data mashups’ or possibly as ‘data dashboards’. Simply put, Thingworx is the IoT platform that makes everything possible. (Here’s exactly what makes Thingworx the leading technology for industrial IoT)
Then you have ThingWorx Navigate.
ThingWorx Navigate is the proper name of PTC’s applications that
ThingWorx Navigate Apps use a Windchill (PLM) connector to extract product data for presentation to Windchill Product Lifecycle Management users.
Fundamentally, ThingWorx Navigate Apps are all simply data and product information mashups created with ThingWorx. With ThingWorx Navigate you receive out-of-the-box apps that are instantly ready to be used with your PLM system. The idea behind these product lifecycle management apps is to ensure users can capture the complete functionality of their PLM (product lifecycle management) investment.
ThingWorx Navigate PLM Apps include:
View Design Files – A design file would be a format of a file that isn’t the native CAD format. This could be a staph or Induce or perhaps a 3D PDF
View Drawing – Allows you to look at just drawings. This application pulls drawings from your Windchill PLM system.
View Part Properties – This feature allows you to look at part properties- as if you were hitting the ‘Information button’ next to a file.
View Parts List – Allows you to look at bills of Materials (BOMs)
View Part Structure– With the View Part Structure App, ThingWorx is actually going into PDMLink and showing different aspects of a specific part instead of different ways of going at it (such as having to open several different tabs to get information). Using this application, you can get all your information together on one page. This feature also includes capabilities that cross-highlight part structures within your product. For instance, you could select a component and it would highlight that part and create a hyperlink that allows you to directly look at that specific part. This feature essentially creates a mash-up that takes information from different places inside of Windchill PDMLink and brings them together putting them on one screen, allowing you to have all your information at your fingertips.
View Document & View Document Structure
If you would like to learn more about ThingWorx Navigate technology or if you have any questions, you can always request to talk with Thingworx Navigate specialists here.
PLM Applications created by EAC
Our EAC Productivity Apps (also known as product lifecycle applications)
They allow departments to access content and perform common tasks through a very simple interface, versus having to use a complex product lifecycle management system (PLM) or Enterprise Resource Planning (ERP) system.
PTC Navigate Apps vs. EAC Productivity Apps
Our EAC Productivity Apps provide capabilities beyond that of the out of the box ThingWorx Navigate apps.
In short, ThingWorx Navigate applications allow you to securely access and present role-specific data from your Windchill system. They provide all of the power of a Product Lifecycle Management (PLM) system to someone who is not familiar with its ins-and-outs of product data management.
EAC Productivity Apps take it a step further by taking the underlying technology of ThingWorx Navigate, and the ability to get at the information in the PLM system and create even more complete applications that really give individuals instantaneous access to the information and product data they need to do their job. EAC’s PLM applications are created using PTC’s ThingWorx IoT platform, however, they can run independently of ThingWorx Navigate.
These apps are unique to EAC.
While built using the same ThingWorx foundation, ADK and [Windchill connector], they have their own look, feel and functionality. These mashups are packaged and sold together as a collection. EAC Productivity Apps created for Windchill promote user adoption and amplify the return on the investment you’ve made in your Windchill system, as well as extending role-based visibility into relevant product data and the impact PLM has on your organization.
Take your product data further with EAC Productivity Apps
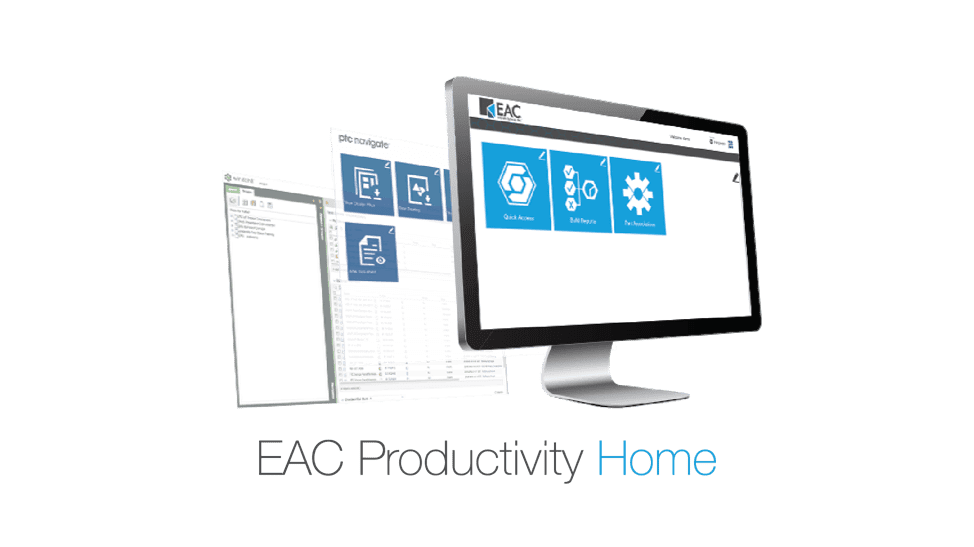
Every subscription of EAC Productivity Apps includes free access to EAC Productivity Home. EAC Productivity Home is a proprietary framework, or launcher, for ThingWorx Navigate applications.
It sits on top of Windchill and
The EAC Productivity App, Quick Search, provides a simple way for users to find content in Windchill. It removes the need for users to apply an understanding of how Windchill objects are related in order to find the information needed to do their job.
The Quick Search PLM application also allows users to search for components and retrieve information and file formats. For instance, if you were to grab a drive system and do a quick search, it’s going to find product information such as parts, EMP like documents, CAD files and more. See EAC Productivity Application Quick Search in action here.
You can also learn more about the Quick Search features in this brochure.
The Quick Access EAC Productivity Application streamlines access to critical and select data sets. Simplifies downstream users feeding critical quality information back to engineering with minimal effort.
This EAC Productivity App allows downstream users to feed critical quality information back to engineering with minimal effort. The simplified interface and consolidated task workflows help users easily submit new problem reports, new change requests, and new variances.
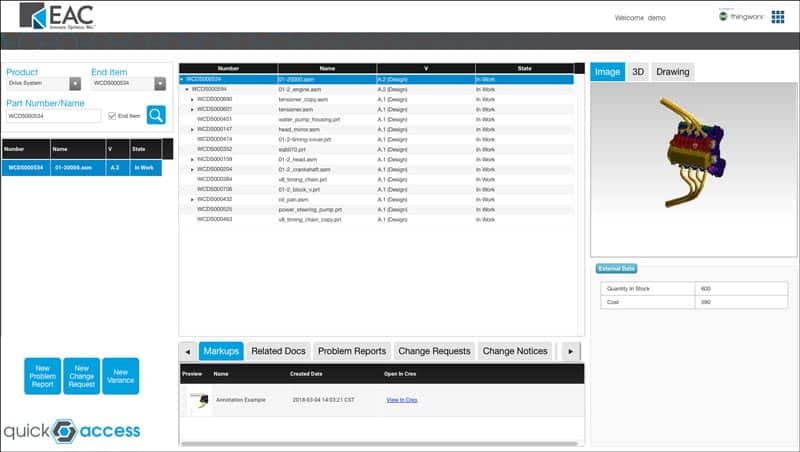
For instance, you could select a component (such as a product), pick its name (the end item number), search for it, and you would get straight to assemblies. With the use of Quick Access users can easily submit new problem reports, change requests, variances and more.
You can learn more about Quick Access features in this brochure.
The Part Associations EAC application provides a “shortcut” for non-CAD users to access critical files and documentation associated with designs like drawings, parts, assemblies, and other documents associated with CAD files and part data.
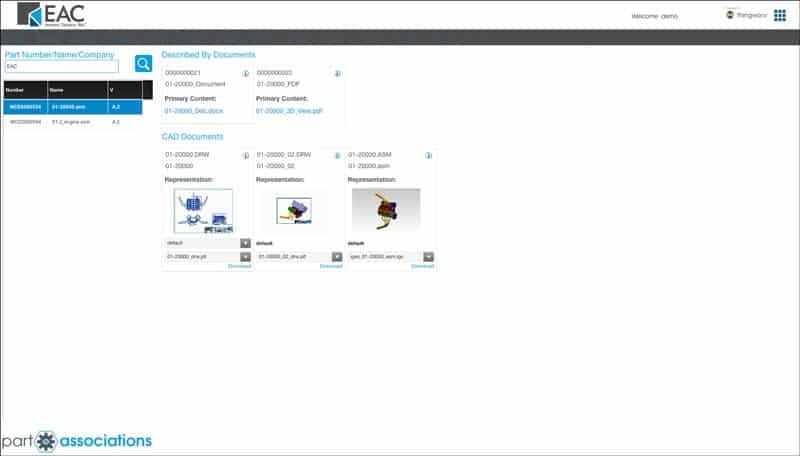
You can learn more about Part Association features in this brochure.
BoM Reports App provides a visual representation of cost
This EAC Productivity App allows users to quickly assess a Bill of Material and ensure projects stay on-time and on-track. The simplified view helps ensure products are built with the appropriate design iterations. With the use of BoM Reports users can easily see BoMs, lists of unreleased parts, parts that have been created or modified by specific users and more.
This app allows users to see the progress of a bill of materials, and apply filters to focus on parts that are not yet released. It is also useful for viewing all of the “make” parts or “buy” parts in a given BoM, or all parts created/modified by a particular user.
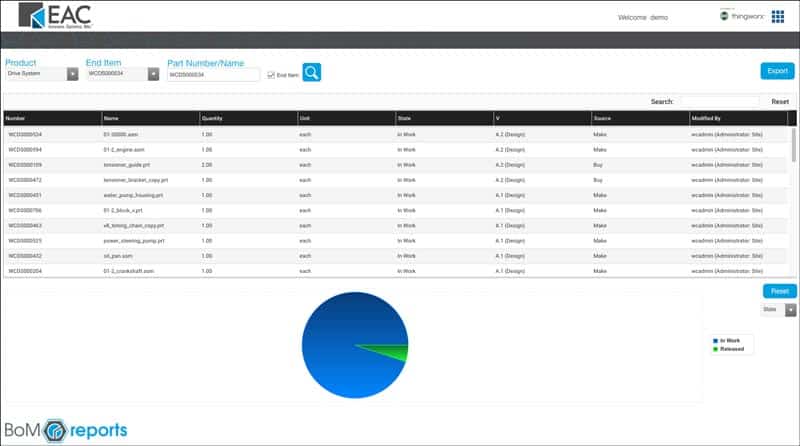
Get better access to your product data
See all the features of EAC P