- rinse station
- 2 rinse buckets
- rinse basket
- rinse bottle
- finishing tray
- tweezers
- scraper
- removal tool
- jig
- flush cutters
- disposable nitrile gloves
In our latest episode of the ‘3D Printing Show’, Anthony Bayerl, Director of Marketing, and Lauren Adey, Additive Manufacturing Specialist bring you the latest news in the 3D printing industry. We have some really interesting news this week including 3D printed sushi, 3D printed homes in El Salvador and on Mars, and a new Draft Resin from Formlabs.
Watch our video to learn about the latest additive manufacturing news.
3D Printed Sushi created from.. urine samples?
3D printed ‘8-bit’ sushi | Image Credit: Open Meals
A company called Open Meals in Japan is doing the unthinkable – 3D printing sushi for its customers. But it’s not just any type of sushi… it’s custom 3D printed sushi… created just for you. Open Meals plan to open their restaurant called Sushi Singularity in Tokyo in 2020 and are looking for people to invest in their concept of digitalized food.
They brought their idea to a tech event called South by Southwest (SXSW) in Austin, Texas just this last year. Their booth wowed onlookers as they demonstrated that they are taking people’s individual chemistry from hair, saliva, or urine samples to create sushi full of custom-tailored nutrients that their body needs. The food is printed in a cube-shape, giving them the nickname ‘8-bit sushi’.
Open Meals booth shows off 3D printed sushi at SXSW 2018 in Austin, TX.
The concept is unique – their idea is to create a healthy meal for you based on your body’s nutritional needs. They send you a ‘health test kit’, you return it with a sample of your choice of bodily fluids, and they’ll send back nutrient-rich edible sushi. Open Meals has a plan to send their customized sushi anywhere in the world, as long as you have a suitable food 3D printer.
3D Printed Concrete Houses for Homeless around the World
3D Printed Housing Community in Latin America | Image Credit: www.dwell.com
By the end of 2019, the partnership plans to house over 400 individuals with around 100 homes in a 3D printed housing community in Latin America. While the average ‘tiny home’ price tag is over $25,000, these 600-800 sq. feet concrete houses can be built for around $4000 in less than 24 hours. The homes themselves are built from locally-sourced concrete to be durable and to sustain weather conditions such as hurricanes or tsunamis.
ICON’s portable 3D printer, called the Vulcan II, is built to withstand real-world conditions and restraints in third-world countries such as power shortages, access to water, and limited labor. With only a few workers needed due to the 3D printer’s remote monitoring technology, the homes are built with almost zero waste and are sustainable for several centuries.
New Story and ICON lead the way for future 3D printed homebuilding.
AI SpaceFactory works with NASA to build homes on Mars
3D printing a community on Mars | Image Credit: AI SpaceFactory
AI SpaceFactory is a company comprised of architectural designers and engineers with a desire to build sustainable and eco-friendly habitats on Earth and Mars. Through 3D printing technology, SpaceFactory has developed a 3D printed vertical home or habitat, called MARSHA (MARS HAbitat), that serves as a livable space for humans on Mars.
The structures are built with a double shell system for isolation from extreme temperature swings and harsh conditions on the planet. The first floor consists of a Mars Exploration Rover docking port, a wet lab, and space hatches for entry/exit; the second floor consists of a dry lab and kitchen; the third floor consists of a bathroom, a garden, a sleeping quarters, and an office space; and the fourth floor consists of a ‘sky room’ for exercise and recreational purposes.
MARSHA considers an optimum mental health environment for humans by including windows on every floor with natural sunlight and artificial lighting that mimics Earth-like light.
According to SpaceFactory, MARSHA habitats are made from a mixture of basalt fiber from Mars rock and renewable bioplastic (polylactic acid, or PLA) processed from plants grown on Mars – which is their plan for agricultural sustainability.
Introducing AI SpaceFactory’s MARSHA habitat for living on Mars.
New 3D Printing Draft Resin From Formlabs
Draft Resin, from Formlabs, for multiple design iterations.
The new Draft Resin is three to four times faster than other Standard Resins giving you the ability to cycle through multiple design iterations at a time. Request a free sample of the Draft Resin to see how the material holds up to your standards.
Lauren Adey, our Additive Manufacturing Specialist, can help you choose the right 3D printer or resin for your needs. Make sure to follow her on LinkedIn to see more additive manufacturing news!
In our new ‘3D Printing Show’ episode Anthony Bayerl, Director of Marketing, and Lauren Adey, Additive Manufacturing Specialist bring you the latest news in the 3D printing industry.
We talk about new product announcements, tips and tricks, product updates, discounts, and promotions.
Watch our video to learn about the latest additive manufacturing news.
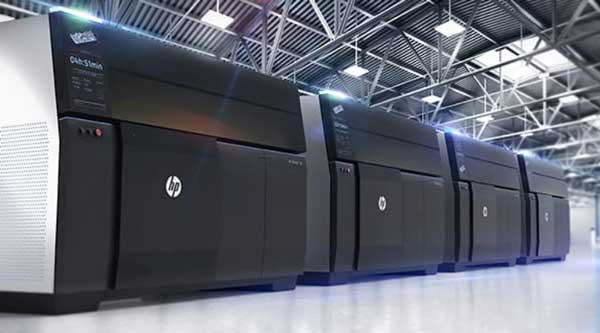
The Future of Metal 3D Printing
Metal 3D printing will pave the way for the future by providing advancements in mass production of 3D printed products such as heat sinks, spare parts, structural components, tooling, medical devices, and industrial automation.
Leading companies like HP are at the forefront of this technology, producing large-scale metal 3D printers that use materials like gold, copper, steel, and titanium to build custom, complex parts.
HP’s article called, Future of Industrial Production: The Metal 3D Printer, points out that we can most likely expect metal 3D printing companies to offer services to print parts and prototypes for other companies in the near future.
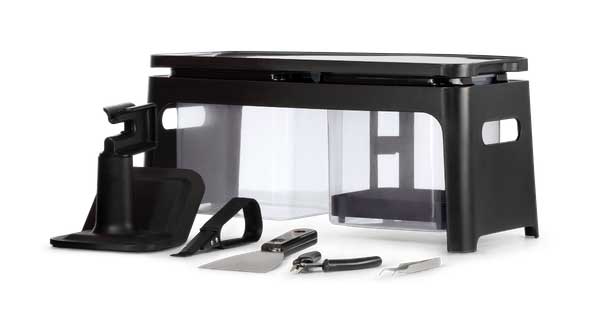
Form 2 Finish Kit
The Finish Kit for the Form 2 helps you stay organized while putting finishing touches on your parts and prototypes.
The Finish Kit includes:
Removing parts after leaving the Form 2 to finish the 3D print overnight
We discuss how Jeff Martin, an Application Engineer from Colder Products (CPC), gives us a tip on how to remove 3D prints from the build platform even when it’s been finished for hours and sitting in the 3D printer.
When you’re printing with material like the rigid resin, it can be difficult to remove if the resin is no longer warm from the finish. Martin suggests using scolding hot water on the surface of the build platform to help scrape off the finished 3D part.
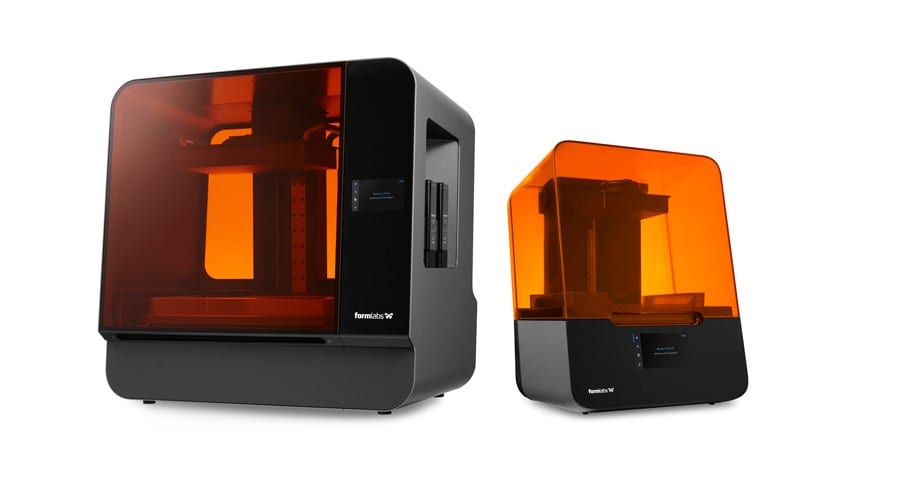
Formlabs Stereolithography 3D Printers: Form 3 and Form 3L
The Form 3 and the Form 3L from Formlabs are here! These 3D printers use a process called low force stereolithography (LFS) for optimum printing details. Read more about the new LFS process in our blog called, Formlabs Releases New 3D Printers using LFS Technology.
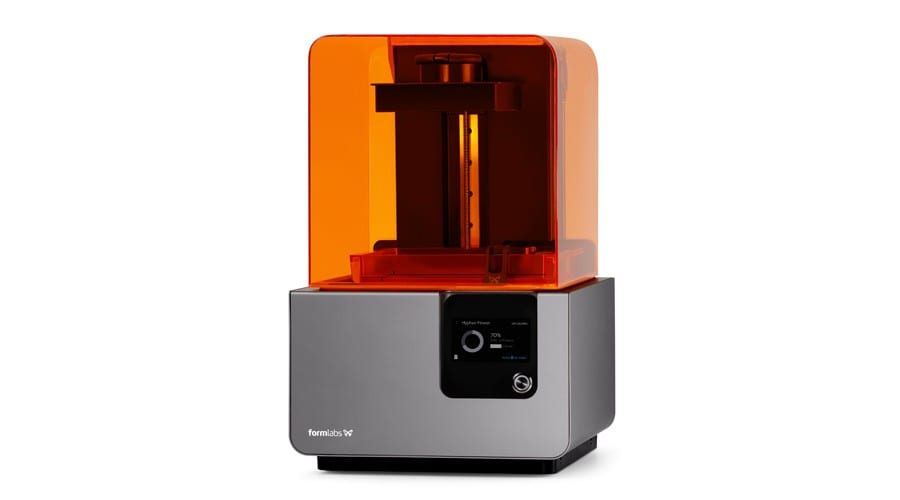
Multiple 3D Printers In-House
In our last post, we mentioned that the Form 2 desktop SLA 3D printer has decreased in price (from its previous price of $3499) to $2850.
If you have always had a print queue, now is the perfect time to buy another 3D printer to use in-house for your parts and prototypes. Now you can excel in rapid prototyping with multiple 3D printers at a low cost.
Read our blog called, 3 Ways 3D Printing In-House Can Transform Your Design Process, to learn how you can benefit from having more than one 3D printer.
Contact Lauren Adey, our Additive Manufacturing Specialist, to take advantage of these special deals! And make sure to follow her on LinkedIn to see more on the latest 3D printing news.
We’d like to share some news with you in our new youtube video we’ve nicknamed the ‘3D Printing Show’. Anthony Bayerl, Director of Marketing, and Lauren Adey, Additive Manufacturing Specialist bring you the latest news in the 3D printing industry.
There are a lot of exciting things happening including new product announcements, tips and tricks, product updates, discounts, and promotions.
Watch our video to learn about the latest additive manufacturing news.
New 3D printer called the ‘Replicator’ makes 3D print in minutes, with almost no wasted material
Stereolithography (SLA) desktop 3D printers, such as the Form 2 from Formlabs, creates 3D prints with photopolymer resin cured with a UV laser and built layer by layer. Structural lattices are created with extra material to ‘fill in’ necessary skeletal-like structures for support to continue to build the part or prototype.
UC Berkeley researchers discovered a new 3D printing technique that transforms liquid on a rotating cylinder to a solid with carefully projected rays of light – without having to waste any extra material in the 3D printing process.
Hossein Heidari, a graduate student at UC Berkeley and co-first author of the work says, “Our technique generates almost no material waste and the uncured material is 100 percent reusable. This is another advantage that comes with support-free 3D printing.”
The researchers named the 3D printer the “replicator” after the Star Trek device that instantly materializes any object. This new technique creates 3D prints in a matter of minutes compared to other techniques that could take hours.
We can’t wait to see where these UC Berkeley researchers take this new zero-waste 3D printing technique!
Creo 6.0 makes software updates to support new lattice structures, build direction, and topology optimization
With the release of Creo 6.0, PTC has updated the additive manufacturing capabilities to design with lattice structures, build direction definition, and slicing. Designing your CAD models with Creo allows you to design, optimize, validate, and run a print-check all in one environment – which means you can send your file straight to the printer when you’re done with your final design. Metal printing capabilities cover around 70% of the metal printers that are sold in the market.
Creo Parametric includes the 3D printing capabilities to directly connect to your printer. These capabilities are included in Creo 5.0 and Creo 6.0.
The Creo Additive Manufacturing Extension includes design abilities such as lattice modeling, advanced beams lattices, custom-defined cells, and defining print build direction. These capabilities are included in the Creo Design Advanced Plus package or you can purchase the extension separately.
The Creo Additive Manufacturing Plus Extension for Materialise includes capabilities to directly connect to metal printers, customize metal support structures, and optimize build direction. These capabilities are included in the Creo Design Premium Plus package or you can purchase the extension separately.
The Creo Topology Optimization Extension includes capabilities to use topology optimization in parts and assemblies and enables geometry reconstruction function. These capabilities are included in the Creo Design Premium Plus package or you can purchase the extension separately.
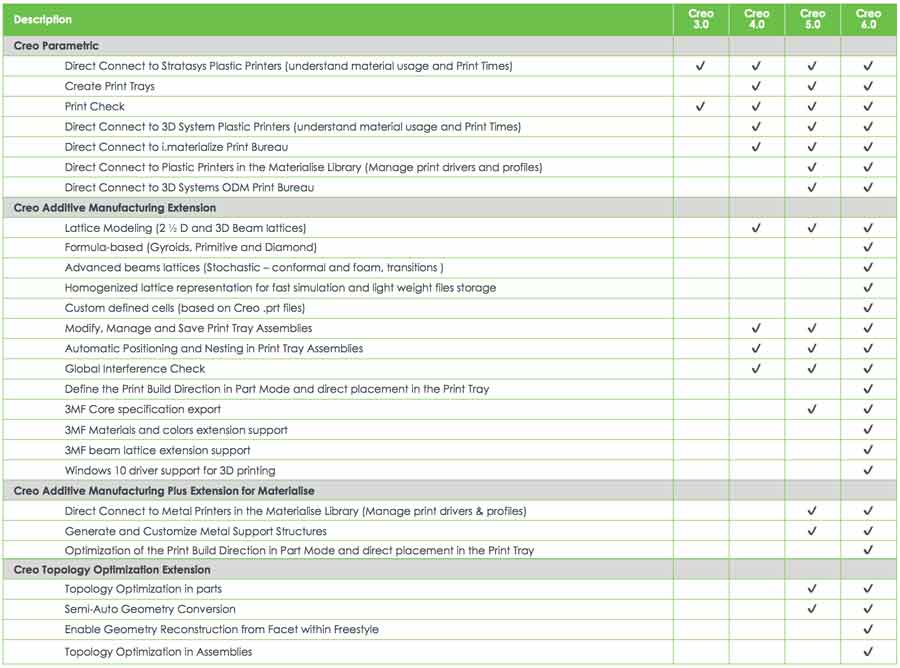
How to wash your parts & prototypes with the Form Wash
We’ve discussed ways that you can better use the products you already own – this time, we’ve got a tip coming from one of our customers – Jeff Martin, an Application Engineer from Colder Products (CPC) on how to clean your parts and prototypes with the Form Wash. Check it out in our blog here.
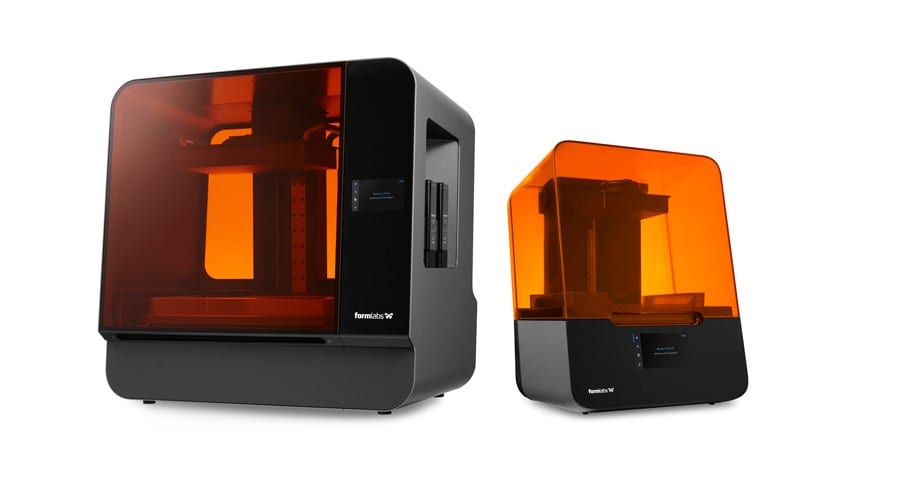
New Formlabs 3D Printers: Form 3 and Form 3L
Formlabs has released the Form 3 and the Form 3L! The Form 2 uses the stereolithography (SLA) process whereas the Form 3 and Form 3L uses a process called low force stereolithography (LFS) – meaning that the printers literally use lower forces to create easier support removal and more precise detail and surface finish. Read our blog Formlabs Releases New 3D Printers using LFS Technology to learn more about SLA and LFS technology.
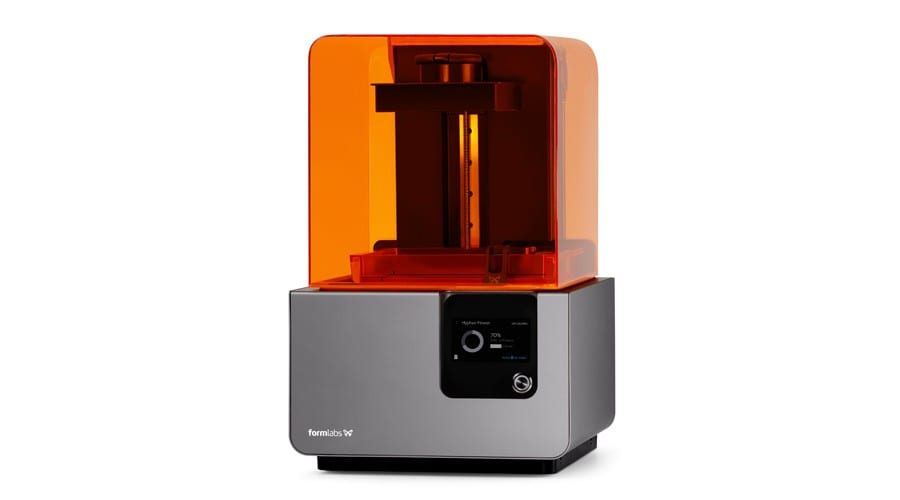
Form 2 Discounts!
The Form 2 desktop SLA 3D printer has dramatically decreased in price (from its previous price of $3499) to $2850. We ARE still selling the Form 2 and will support those that want to purchase an already affordable 3D printer at a more affordable price.
Contact Lauren Adey, our Additive Manufacturing Specialist, to take advantage of these special deals!
The Form Wash is designed for the Form 2 3D printer from Formlabs to automate the cleaning process between printing parts. It makes things much easier for engineers who don’t want to waste any time cleaning their prototypes so they can either use the Form 2 again for another print job or get back to their next project.
Washing printed parts before post-curing helps to remove excess residual resin from part surfaces and cavities. Formlabs suggests using isopropyl alcohol (IPA) as the solvent that is most compatible with washing.
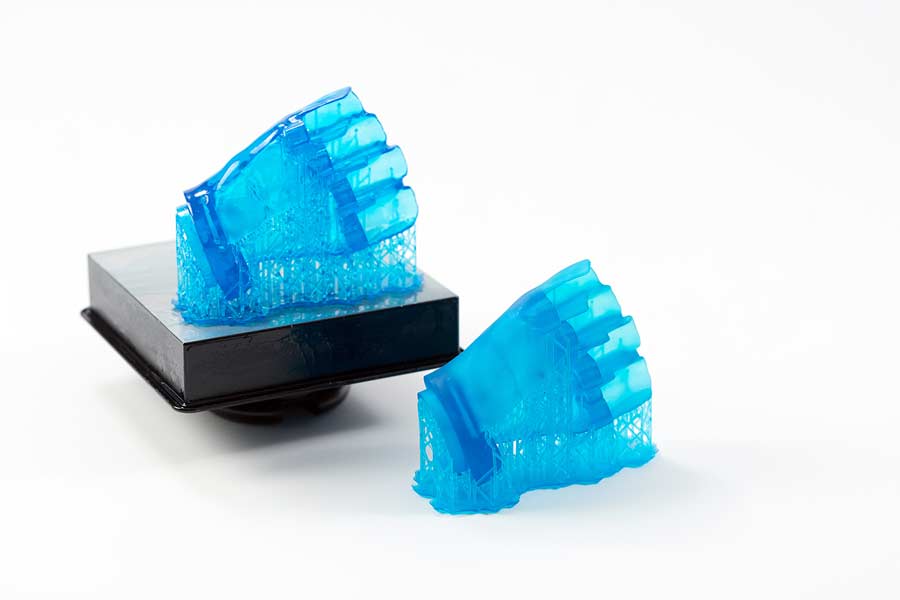
If you take a look at the image above, you can see that the left part is much cleaner and visually is more detailed than its counterpart. After using the Form Wash, you can typically use the Form Cure to expose printed parts to light and heat to stabilize the parts for performance. Using the Form Cure is not necessary but using the Form Wash and Form Cure together is recommended for optimal finishing.
Colder Products Company (CPC) has trusted EAC for years to provide them multiple Form 2 printers and other Formlabs equipment and materials to rapidly prototype customized quick disconnect couplings, fittings, and connectors for plastic tubing used around the globe. We answer a few questions that users have about the Form 2 and also include an engineer’s intake as well. Here is how Jeff Martin, an applications engineer at CPC, uses the Form Wash in-house to reduce time spent cleaning 3D printed parts.
How much time does it take for one wash?
Formlabs says that most resins require washing for the Form Wash default programmed time, which is 10 minutes – although additional time is needed for some resins. The following table shows Formlabs’ recommended wash times for each resin being used.
Resin | Wash Time | Resin | Wash Time |
Tough | 20 min | Elastic | 10 min + 10 min |
Rigid | 15 min | Dental SG | 5 min |
Grey Pro | 15 min | Dental LT Clear | 5 min |
Castable | 10 min | Denture Teeth & Base | 10 min |
Castable Wax | 10 min | Ceramic | 5 min |
High Temp | 6 min | All other resins | 10 min |
Jeff suggests that you should set your wash time at 20 minutes for each wash. He also recommends that it’s best to physically have 2 Form Washes in-house to speed up the cleaning process, “The first Form Wash set to 10 minutes to wash parts hanging from the build platform, and the second Form Wash is used to clean the parts broken free from supports.” (Keep in mind, he typically uses Rigid Resin for his 3D prints).
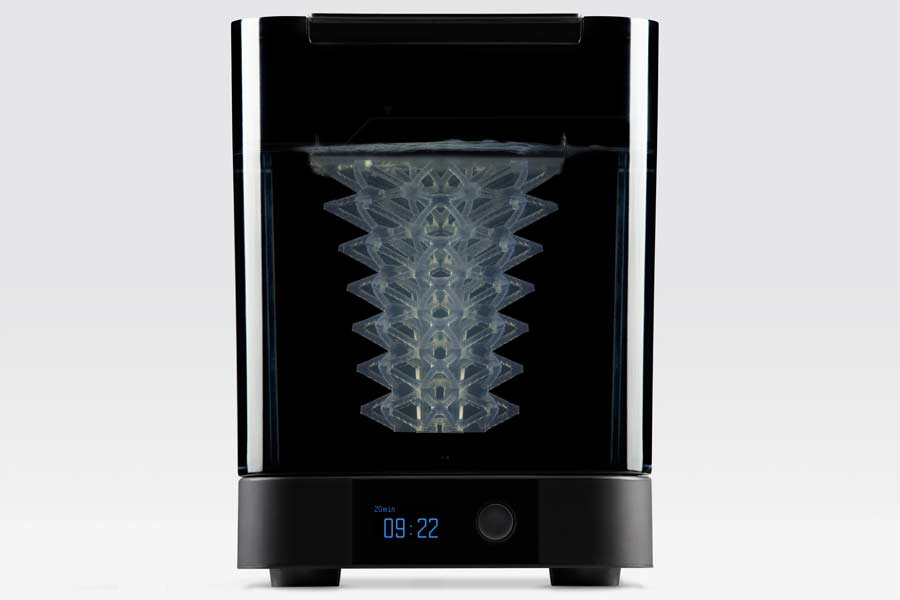
What’s the best way to wash prototypes?
If you’re using the Finishing Kit, Formlabs recommends that you should wash your prototypes in at least two standard wash tanks – the first wash, being the ‘dirty’ wash, would take 10 minutes and then the second wash, using a cleaner tank, for another 10 minutes. Once the first tank gets dirty, you can dispose the IPA, transfer the second tank into the first tank, and then pour new alcohol into the second tank.
The Finishing Kit includes 2 wash tubs to manually clean your 3D prints – whereas the Form Wash automatically cleans your parts and prototypes.
Jeff says the advantage of having a second Form Wash is that you can use Formlabs’ same theory of having a clean tank to do the final rinse. “I find it in my experience to be extremely useful to remove the supports for the second wash. The reason is that the supports block the fresh circulation of clean solvent from the parts. You will notice that for deep aspect bores and blind holes, if you do not remove the supports, they often times will not fully be cleaned of resin. After removing the supports and letting the parts bounce around in the basket during the last 10 minutes, they will always come out clean.”
Learn more FAQ by reading our related blog, “Everything You Need to Know About the Form 2 3D Printer.” If you’re interested in a free sample, then contact us at your earliest convenience.
Also, follow me on LinkedIn for tips and tricks on how to use the Form 2 and other equipment and materials from Formlabs!
You can now find the softest material for 3D printing, Formlabs’ Elastic Resin, and the most pliable of their library of Engineering Resins available to purchase through national commercial reseller EAC Product Development Solutions.
Request a free sample part to see how soft and silicone-like the Elastic Resin feels.
Elastic Resin
The Elastic Engineering Resin has a 50A Shore durometer material suitable for prototyping parts normally produced with silicone. This soft stereolithography (SLA) resin is highly elastic, yet strong enough that it doesn’t tear during the print job. Usually, these types of flexible prototypes have to be produced with mold making, but the Form 2 makes it possible to produce these models in a matter of hours in-house.
You can use Elastic Resin for parts that will bend, stretch, compress, and hold up to repeated cycles without tearing. Typical key applications for soft silicone and urethane parts include wearables and consumer goods prototyping; medical visual simulation and devices; compliant features for robotics; and special effects props and models.
This new resin is a long-lasting, tear-resistant, and made of resilient material that can withstand repeated use. It should be noted that soft 3D printing materials, in general, require denser support structures and attention to specific design guidelines before you print.
Real-use applications in various industries
Medical Industry: The Elastic Resin is translucent – a color ideal for medical visual applications and device prototyping. Anatomical simulation models, artery and vessel models, prototyping silicone parts.
“Elastic Resin’s opacity illuminates internal cavities well and its durability means that educators, trainees, and clinicians can handle and examine models without the worry of breakage. This material will be of particular interest to cardiovascular surgeons and interventional radiologists, as well as those conducting fluid dynamics studies and working in catheterization labs. It is relatively cost-effective when compared with other similar materials on the market, which can only help accelerate the adoption of 3D printing in medicine.” -Sanjay Prabhu, MBBS, FRCR; Pediatric Neuroradiologist and Clinical Director, SIMPeds3D, Boston Children’s Hospital
Engineering and Product Design: For those that are using Flexible Resin already, the Elastic Resin is a softer option for consumer product development. Prototyping silicone parts and seals, soft pads, grips, and ergonomic features, as well as sports eyewear.
Comparing the Elastic Resin to the Flexible V2 Resin for engineering and product design applications:
Elastic | Flexible V2 | |
Durometer | 50A: a soft flexible material | 80A: a hard flexible material |
Elongation | High (160%) | Medium (80%) |
Energy return/ spring back | High | Moderate |
Tear Strength | Better (19.1 kN/m) | Prone to tearing (13.3 kN/m) |
Reaction to compression | Good energy return/spring back | May break |
Color | Translucent | Dark Grey |
Print resolutions: 100 microns only. Post-curing required. LT Tank Required. Good elongation (160%) and tear strength (19.1 kN/m). Wash time: 20 minutes. Cure time: 20 minutes at 60 °C.
Price: $199/L
Learn more about the Form 2 on our website. Or contact us about ordering the Elastic Resin.
The technology behind most resin 3D prints is referred to as stereolithography (SLA). The additive manufacturing technology converts liquid materials into solid parts by curing each layer with a light source in a process called vat photopolymerization. The light source is usually a UV laser or projector that cures the liquid resin into hardened plastic. SLA printing is considered to be one of the most widely used techniques in producing high-quality 3D prints such as models, prototypes, and production parts.
Why choose a desktop SLA printer?
The closed build environment and heated resin tank provides consistent conditions and better accuracy for each print. SLA creates parts with a smooth surface finish as soon as it’s done printing which is ideal for applications that require a flawless finish. It helps reduce finishing time as well since the parts can be easily sanded, polished, and painted. The smallest detail is much finer on SLA printers due to the 140 micron laser spot size on the Form 2 compared to 350 microns on industrial SLS printers and 250-800 microns on FDM machines.
In-house 3D printing can reduce costs by 50-90% when factoring in consumables, maintenance, labor, and depreciation of the machine. There is a turnaround time of hours instead of days or weeks with outsourced production. Desktop SLA 3D printers allow for accurate prototypes, rapid iterations, and earlier discovery of errors which all lead to better final results.
Formlabs – ‘Form 2’ Desktop SLA 3D printer
The Form 2 delivers high-resolution SLA prints that are significantly smoother and more detailed than other plastic 3D printing technologies. It enables you to print precise models with a smooth surface finish and helps save time and money during the design and manufacturing process.
Automated Resin Refill
Level sensing ensures your tank is automatically filled during printing. No more pausing for manual refills.
Resin Cartridge Recognition
The Form 2 automatically recognizes the resin type, configures settings, and allows you to keep track of resin supplies from your Dashboard.
Open Mode
Experiment with non-standard applications such as embedding objects in prints, creating lithopanes, and etching PCBs. It enables support with 3rd party resins.
Form 2 – SLA materials for different industries
Every industry has specific needs and applications for 3D printing. The stereolithography materials selection for desktop SLA 3D printers are built to address these varying needs of design and engineering groups.
Standard
Standard resins are ideal for rapid prototyping, product development, and general modeling applications. The resin provides high resolution, fine features, and a smooth surface finish and doesn’t require post-curing. The resins are available in greyscale, clear, white, and a color kit.
Engineering
Engineering resins are used to create functional parts for anything from assemblies to injection molds and have tough, durable, flexible, and temperature-resistant characteristics. They are used to simulate a range of injection-molded plastics to help designers and engineers conceptualize, prototype, and test final products.
Dental
Dental materials have specific applications that include orthodontic models, splints, retainers, diagnostic, biocompatible surgical guides, and educational models. These resins allow dental labs and practices to create a range of dental products in-house based on a patient’s intraoral scan or CBCT scan.
Jewelry
Jewelry prototypes can be made with SLA technology to create a fitting ring or try on piece. Castable resin is designed for direct investment casting to allow jewelers and casting houses to view the 3D print in-house or to create custom jewelry cost effectively.
Learn more about the Form 2 3D printer here or request a sample part here.